Lithium batteries have become a cornerstone of modern solar energy storage, offering high energy density and long lifespan. To ensure their efficiency and reliability, the production process of lithium battery packs involves several steps. Now, we will walk you through each stage of the process:
1. Applying Barley Paper to the Positive Electrode
One key enhancement to lithium battery pack production involves the meticulous application of barley paper onto the positive electrode of battery cells. This seemingly simple step plays a vital role in reducing internal short circuits caused by incorrect welding during electrode attachment. There are two primary methods for applying barley paper:
- Method 1: Manual Application
- Method 2: Fully Automatic Barley Paper Machine
2. Cell Sorting and Grouping
Achieving uniformity among battery cells is paramount to a battery pack’s overall performance. Battery automatic sorting machines efficiently group cells based on their characteristics, preventing mismatches that can lead to performance disparities and safety concerns.
E.g. 51.2V lithium battery module(usually refer to 48V) consist of 16 lifepo4 battery cell(3.2V per cell * 16=51.2V) by series junction
3. Battery Pack Welding
Battery pack welding involves the secure attachment of components, and there are two prominent methods:
- Method 1: Manual Welding
- Method 2: Fully Automatic Spot Welding Machine
4. Welding Battery Pack Protection Boards
To safeguard the integrity of the battery pack, protection boards must be accurately attached. This step can be accomplished manually or using a fully automatic single-sided protective plate spot welding machine.
5. Semi-Finished Product Insulation
Ensuring the safety and stability of the battery pack involves insulating voltage acquisition lines, wires, and output lines. Proper use of materials like high-temperature adhesive tape, barley paper, and cable ties is essential.
6. Semi-Finished Product Testing
Before completion, a battery pack with an added Battery Management System (BMS) undergoes thorough testing. Routine tests include charge and discharge assessments, internal resistance measurement, capacity evaluation, and more.
7. Lithium Battery Pack Packaging
Packaging methods vary based on the design and configuration of the battery pack. Regardless of the approach, careful handling is crucial to avoid damage during this phase.
8. Comprehensive Testing of the Assembled Pack
The fully assembled battery pack undergoes rigorous testing to verify its performance and safety. This step includes checking key parameters such as voltage, internal resistance, and charge/discharge behavior.
9. Final Packing and Shipping
As the battery packs are prepared for distribution, proper packaging techniques are employed to ensure they reach their destination intact and ready for use.
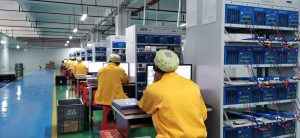
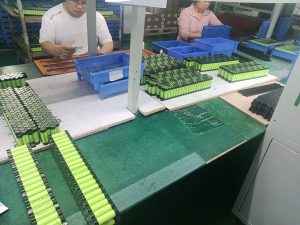
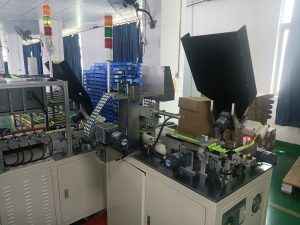
This guide provides an in-depth look into the process of producing lithium battery packs, showcasing the dedication and technology that contribute to the creation of high-performance energy solutions, power our modern world from the endlessly solar energy.